文系社長の"モノづくり人生"
橋本秀夫(日本エクシード) 第3回「自主独立!」
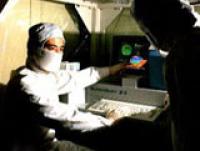
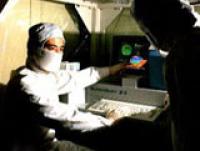
技術進化に隔世の感
橋本が自ら望んで現場作業に入ったのは、かれこれ30年以上前のこと。橋本は当時をこう振り返る。
「IC基盤の研磨は凄く魅力的な仕事でしたね」
材料がまだゲルマニウムからシリコンに代わってあまり時が経っていない頃だった。
「シリコンの基板を研磨加工できるメーカーは日本には他に無かったので、日本エクシードは町工場とはいえ脚光を浴びていました。だからやっている仕事に非常に興味と魅力を感じました。そうでなければ多分この会社に就職しなかったと思うんです」
この間の研磨加工技術や半導体技術の進歩には著しいものが有り、今振り返ると隔世の感があるという。
「現在、シリコンウエハのサイズは300mmが主流になってきましたが、当時は50mmが中心でした。研磨方法は光学レンズ研磨技術の応用です。今思えば、よくあれでICが正常に作動したものだと妙に感心してしまうことが多々あります」
「天然の松脂でウエハを貼り付け、怪しげなパウダーで研磨したあと、水道水で研磨剤を洗い落としたりと、いかにも原始的な方法です。それからウエハを基盤から剥がし、トリクロールエチレンなどの有機溶剤で洗浄し、フロンで蒸気乾燥させるのです。研磨装置に至っては、光学式の恐ろしく生産性の悪いもので、仕上げ用の研磨盤には光学用のピッチ皿を使い、研磨室になると二重構造の窓枠とはいえ鉄製や木製だったため、風の強い日には遠慮なく砂埃が入り込みました。もちろん、空調はごく普通のパッケージ型エアコンで、クリーンルームなんて考えも及ばないような状況でした。当然、半導体加工用のエア管理なんかできていません」
変わらない精度出し匠の技
半導体業界や研磨業界では微細加工技術への追求が進み、ウエハにも平坦度や清浄度への要求が飛躍的に高まってきた。こうした背景から研磨加工の方法にも目覚しい進化が見られたという。
「例えば出荷するウエハに付着する汚れのレベルを比較しますと、当時は目視のみで合否が判定されていました。今では目視では検出できない0.1μmクラスの付着物や原子レベルでの金属汚染を数値化した規格が設定されています。ですから作業衣は爪先から頭のてっぺんまで完全に包んでしまうので、髪の毛1本落下しない。まるで宇宙服を着ているような防備です。作業室は当然、全てクリーンルーム。洗浄で使う超純水は殺菌装置を通過させるのでランニングコストはべら棒に高くついてしまいます」
この話から先端産業の一翼を担う研磨加工のかなりの作業が装置化・電子化されたことが窺える。しかし、橋本は「装置や加工素材の微妙なクセを見抜いたり、精度出しの基本的な力量は、匠の技が不可欠なことは30年前と何ら変わりがありません。だからこそ超平坦・超平滑・超清浄・超薄化という5つの超を技術と技能により、研磨の世界を極めることができたのです。漫然と作業していると、技術的に"置いてきぼり"を食ってしまいます」と、最後の決め手は人材とその人たちが長い期間をかけて培った匠の技にあることを強調する。
研磨加工の技術進化は、クリーンルーム、製造装置、検査装置など、最新鋭設備の導入などに莫大な資金が必要である。
「先端産業というのは半導体や携帯電話のように生産規模も大きくなってきますし、要求される精度も高まります。装置そのものも機能的にすぐ陳腐化し、あっという間に買い替えの時期が来ます。並の投資じゃやっていけなくなる。同業者が、大手取引先の傘下に入らざるを得ないワケはそこにあるんです」
そんな厳しい業界で、なぜ日本エクシードは自主独立を堅持していけるのか。誰もが思う疑問だ。橋本は次のように説明する。
「当社は材料やデバイスメーカーより高い技術があると自負しています。彼らも当社に発注せざるを得ないんです」
だが、技術力を誇る同社には有効な特許技術というものが皆無である。あるのは長年培った研磨加工に関する数々のノウハウと、それを活用する技術者・技能者集団だけだ。そして、ノウハウを護り後輩達に伝承する日本エクシード独自の知的財産戦略が今始まろうとしている。(敬称略)
掲載日:2006年11月27日