Be a Great Small
革新的な切削工具を開発し、海外で特許を取得「西研株式会社」
2023年 7月 18日
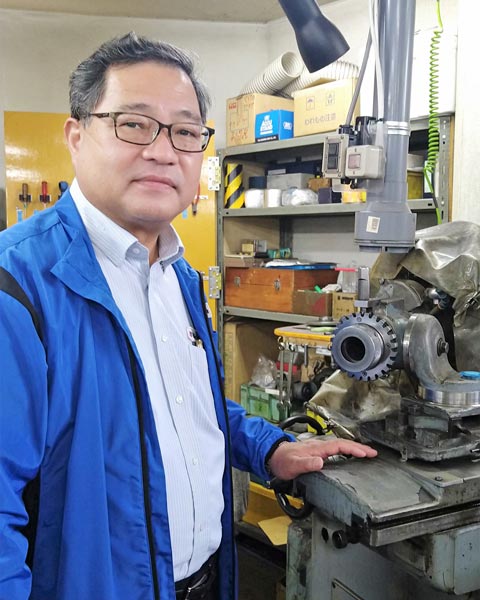
広島市西区で切削工具の再研磨や加工事業を手掛ける西研は2020年、高精度の深穴加工を可能にした世界初の切削工具「クレアボーラー」を開発した。これまで特殊なNC工作機械が必要だった深穴加工を一般的なNC工作機械でも可能にする画期的な切削工具だ。日本のほか海外6カ国でも特許を取得。2023年には第29回ひろしまベンチャー大賞を獲得した。
2人でスタートした再研磨のビジネス
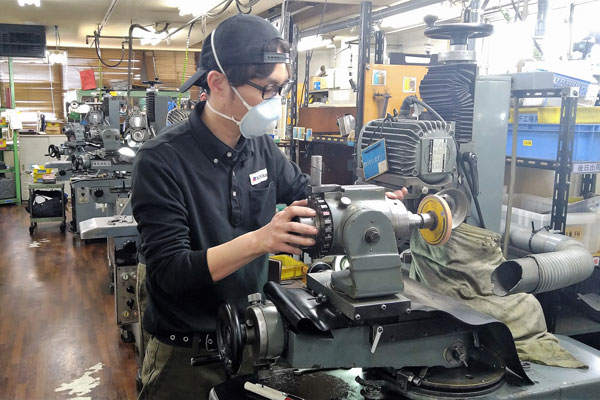
「切削工具の加工・製造を始めてから、自分たちに価格決定権のあるものを作りたかった。メーカーとして自立し、自社のブランド力を世の中の人に知ってもらうようになる。その足がかりになるものをつくることができた」。西研社長の寺本博氏は、新たに開発した「クレアボーラー」を手にしながら胸を張った。
創業は1995年。同じ会社に勤めていた同僚と2人で切削工具の再研磨を請け負う会社を立ち上げた。資本金は300万円。汎用の工具研削盤2台からのスタートだった。
再研磨は、摩耗して切れ味が悪くなったドリルやエンドミルなどの切削工具を研ぎ直すサービスだ。一見すると、単なるドリルのように見える切削工具は、金属やプラスチックの材料を削り込み、思いのままの形を作りあげる。硬い材料を何十、何百と削り込むと、切削工具の刃は1日ももたず数時間ほどで摩耗してしまう。このため、部品などの加工メーカーは、西研のような専門業者に摩耗した工具の再研磨を依頼。切れ味を回復させて再び加工に使用している。
寺本氏によると、取引先のもとに週に1度定期的に顔を出し、摩耗した切削工具を引き取り、研磨機にかけ、再び新品同様の切れ味に戻して顧客に納品するという。「これまでにいろいろな仕事を経験してきたが、理髪店のように取引先が定期的に来てくれるような仕事をしたかった」と再研磨のビジネスを始めた理由を話してくれた。
「NOと言わない会社」を目指し、顧客の要望を最優先に営業を展開。金曜日に「休み明けには納品してほしい」と引き受けた仕事を休日返上で対応することもいとわなかった。顧客優先のサービスは高く評価され、市内を中心に取引先の数は増えた。最新の装置も導入。従業員を雇い、事業の規模は少しずつ大きくなっていった。
切削工具の製造にチャレンジ
やがて再研磨だけでなく、切削工具の新作にもチャレンジする。2002年にNC工具研削盤を導入。当初は一般的に広く利用されている切削工具を製造した。だが、数多くの大手メーカーが製造・販売する競争の激しい商品。なかなか思うような価格で販売することができなかったそうだ。
一方で、「再研磨」のビジネスには逆風が吹き始めていた。東アジアを中心に低価格の切削工具が国内に出回るようになったという。「再研磨に出すよりも買った方が安い」と切削工具を使い捨てする加工メーカーも増えてきた。業界全体が下降線をたどる中、2007年のリーマンショックが追い打ちをかけた。同業者の廃業が増え、西研の経営も厳しさを増していた。
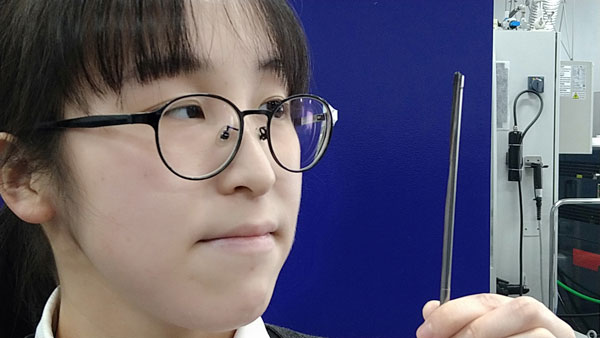
そんな中、2017年にチャンスが訪れた。
再研磨のビジネスの傍ら、取引先のニーズを応じて、特注の切削工具の加工を請け負ってきたが、つきあいのあった取引先から「加工メーカーがタービンの羽根を削る切削工具のコンペをやるので参加したらどうか」と紹介された。
チャレンジすると、西研が提案した工具が採用された。「海外のトップクラスのメーカーも参加していた。海外メーカーが1位で、僅差の2位だった。これでちょっと自信がついた」。
これを機に商社や取引先などからいろいろな相談が寄せられるようになった。「こんなものは作れないか」「こんなことはできないか」。相談の一つが「まっすぐ深い穴を開けられるドリル」だった。
「深い穴をまっすぐ開けるのなんて単に切削工具を長くすればいいと思うかもしれないが、簡単ではなかった」と寺本氏。深い穴を開けようとすればするほど100分の数ミリ単位でズレが生じやすくなる。材料の奥深くを削る刃先に冷却液を送り込む方法を考える必要もあった。冷却液が届かないと、加工ポイントが発熱して工具を破損させる原因になるからだ。
開発スタッフがさまざまな工具の形状を考え、材質などを検討。試行錯誤を繰り返し、3年半をかけて実用化にこぎつけた。「最初の半年は、試作品を試すたびぽきぽきと折れた。2年くらいでだいたいの形ができた。残りの1年半は、どうすれば安定した生産ができるかとか、最もいい切削条件を検証するのに費やした」と開発担当者は説明する。
他の工具にはない画期性
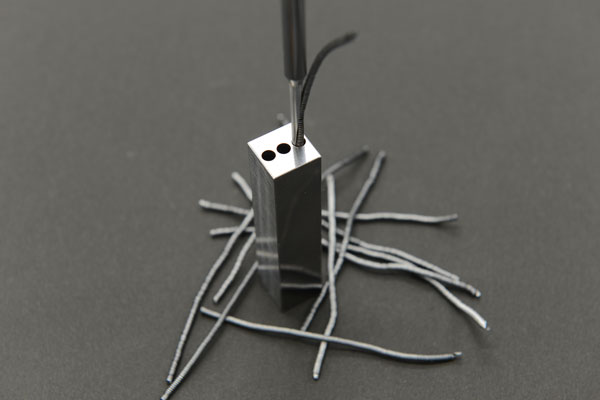
そんな苦労を重ねて完成した「クレアボーラー」の形状は、他の切削工具にはない特徴を持っている。
直径2~8ミリの小さい深穴を加工する工具だけあってとても細長い。構造は刃先、胴体、シャンク(柄)の3つから構成され、刃先より胴体がわずかに細くなっている。切れ刃は1枚刃で、切りくずを排出するためのU字型の溝が深く設けられている。
一般的なドリルは、穴を開ける際に出てくる切りくずを自然と外に排出するような仕組みになっている。しかし、その影響で外部から冷却液をかけてもその仕組みに邪魔されて、刃先に届く前に逆流してしまう。一方、クレアボーラーは刃先よりも胴体を細くしたことで生まれる「すき間」から胴体冷却液が入り込む。刃先に設けられた特殊な形状の溝がポンプの役割を果たし、加工ポイントを冷却する仕組みになっている。
また、一般的なドリルでは、切りくずの排出性を向上させるため、切りくずをバラバラにする切れ刃形状が主流になっているのだが、刃先の摩耗で切れ味が低下したりすると、ちょっとしたきっかけで切りくずが詰まってドリルが折損することがある。だが、クレアボーラーは1本につながった状態で穴から排出されるよう切れ刃形状を変更。切りくずが詰まって折損するリスクもなくなった。しかも、刃先が常に穴の中心を探り加工するように工夫を凝らし、抜群の真円度、真直度を実現した。加工する材種によるが、刃の直径の20倍もの深さの穴を開けることができる。
日本のほか6カ国でも特許を取得
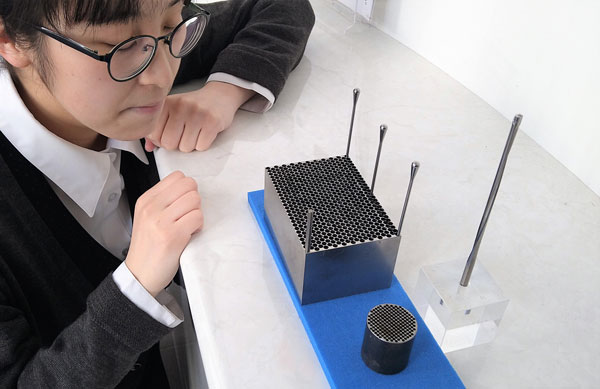
「今までにない形状なので、ちょっと特許に出してみようか」
開発を進める中で、寺本氏は切削工具に詳しい大阪の特許事務所を訪問した。門前払いされるのを覚悟していたそうだ。弁理士からは最初に「ドリルだけで1万種類以上の特許がある」と言われた。だが、クレアボーラーの模型を見せて詳しく説明すると、弁理士の目の色が変わった。「これは確かに見たことがない」。
2018年秋に革新的な9つの要件を申請し、2020年に日本の特許を取得した。さらに弁理士のアドバイスを受け、海外の特許にもチャレンジ。ジェトロ(日本貿易振興機構)の補助金を活用し、米国とイスラエルのほか、欧州のドイツ、イタリア、フランス、スウェーデンの計6カ国に申請し、22年には申請したすべての国の特許がそろった。
クレアボーラーの大きな特徴は、一般的に使われているNC工作機械に取り付けるだけで深穴加工が可能になる点だ。深穴加工には、冷却液を切削工具の中から流し込む内部給油装置のある工作機械でしかできなかった。だが、クレアボーラーがあれば、中小の製造業者でも新たな機械を導入することなく加工ができる。中小のメーカーにも加工を請け負うチャンスが生まれる。
一方で、「これからの課題は、どうやって市場を開拓していくか」と寺本氏は話す。特殊な加工に使われるものなので、具体的にどういったものづくりに活用できるのか、なかなか提案しにくいところがあるという。そこで、これまでにクレアボーラーを購入した顧客をリサーチしながら、部品加工のメーカーなどに活用を提案し、売り上げの拡大につなげていく考えだ。
「手本となる会社になる」を目標に
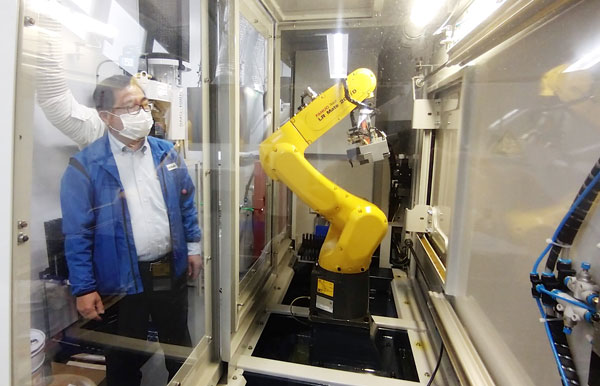
ものづくりにチャレンジする中で、寺本氏の経営に対する考えは少しずつ変化していったそうだ。
「『NOと言わない会社』ではなく、『NOと言える会社』を目指そう」という。切削工具の加工へのチャレンジを始めたころに知人の紹介で中小企業家同友会に参加。定例会や勉強会で経営のノウハウを学び、大きな刺激を受け、そう考えるようなった。
「勉強会で学んだいいものは持ち帰って実践した。1TTP…徹底的にパクっている」と笑った。「NOと言える会社」づくりには、NOと言わず、社員たちに負担をかけてきたことへの反省も込められている。価格決定権のある商品を開発し、取引先に対して優位な立場で交渉する。そうすることで、社員に無理な負担をかけず、働きやすい職場にする。今の時代にかなった目標だ。「今は他の手本となるような会社になりたい」と寺本氏は語る。
「理髪店のような仕事」を目指し、たった2人でスタートした小さな会社を海外で特許を取得できるまでに成長させた寺本氏。新たなチャレンジが会社をどう変えるのか注目される。
企業データ
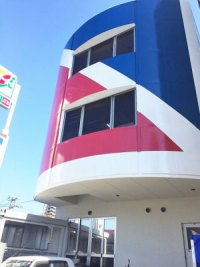
- 企業名
- 西研株式会社
- Webサイト
- 設立
- 1996年3月
- 資本金
- 3000万円
- 従業員数
- 20人
- 代表者
- 寺本博 氏
- 所在地
- 広島県広島市西区大芝1-7-12
- Tel
- 082-230-9100
- 事業内容
- 切削工具の再研磨・加工・製作、及びコーティング、機械工具等の販売