生産性を考える-IoTとものづくり企業-
独自生産管理システム、IoTトレーサビリティーシステム「山口製作所」
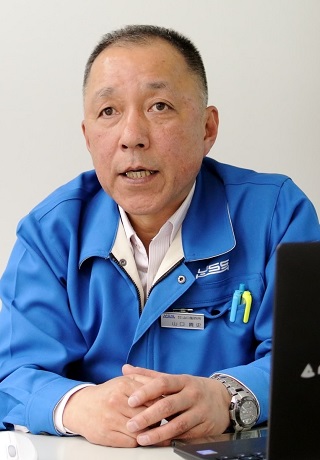
金型製作から金属プレス加工までを一貫して手掛けるメーカーで、早くから社内のOA化、IT化を推進。現在、生産現場の各種工作機械・測定機をはじめ、タブレット、パソコン、プリンターなど100台以上のクライアントを一つのサーバーで一元管理する社内ネットワークを構築しており、「受注1件のデータ処理は1回の手入力で済ませる」を目標に独自開発した生産管理システムを稼働させている。さらに、IoTを活用して複数のプレス機の稼働状況をトレーサビリティーできるシステムの開発・導入を進めており、同業他社との差別化に役立てる考えだ。
独力で社内システムを開発
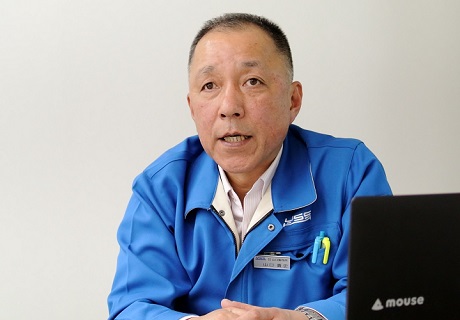
プレス加工・金型メーカーの山口製作所が社内でコンピューターを使い始めたのは1989年に遡る。その2年前の87年に、創業者である父親の急逝を受けて代表取締役社長に就任した山口貴史(やまぐち・たかし)氏(53)が旗振り役となってきた。
山口社長は当時、大学を卒業し、後継者になることを前提に地元の専門学校に通い始めていたところだったが、急きょ、入社を繰り上げて経営者になった。その経営者の仕事にも慣れ、ある程度余裕ができた頃に、自分が学生時代に父親に導入を勧めたパソコンがほこりをかぶっているのを見て、「せっかくだから」と、プログラミング言語の「COBOL(コボル)」を勉強しながら社内のOA化、IT化に取り組んだ。
「字が下手で、伝票を書くのが嫌だった」(山口氏)こともあり、最初に納品書の発行作業をパソコンでできるようにした。当時の同社の製品は、納入先からジャスト・イン・タイムを要求される自動車部品が多く、納入期日などを細かく指定されるので、そのぶん納品書の枚数も多くなりがちだったからだ。ただ、多額のコストをかけられないので、山口社長自ら勉強しながらプログラム作成に取り組んだところ、取引先の専門知識を持つ人が手伝ってくれたこともあり、狙い通りのシステムが完成。以来、社外のシステム開発会社を頼ることなく、独自開発を基本に、順次、OA化、IT化を進めてきている。
1991年にはOS(基本ソフト)にマイクロソフト社の「MS-DOS」を使った在庫管理システムの運用を開始。95年には新登場のOS「Windows(ウィンドウズ)」を使って社内ネットワークを構築した。さらに96年にはデータベース管理ソフト「Access(アクセス)」による生産管理システムを開発し、運用を始めた。続く97年には無線LANを導入。生産現場でも98年にCNC(コンピューターによる数値制御)測定機、2000年にCAD/CAM(コンピューター支援による設計・製造)を相次ぎ導入し、社内ネットワークに連結してきた。
製造現場のIoT化も2008年と早い。プレス機のサーボモーターの駆動データをインターネットで送れるようにした。現在は、プレス機の荷重管理システムの開発・導入を進めている。複数台のプレス機の状態をIoTシステムを活用して一括管理することで、金型の最適なメンテナンス時期の予測、異常加工の検出、加工手順の標準化などにつなげ、生産性向上を図る考えだ。
手入力を極力減らす

この間、顧客からファクシミリで送られてくる発注書をプリントアウトしないで、電子データのまま自社の受注管理システムに送信するなどにより、ペーパーレス化も推進。2008年の時点で年間約8300枚にのぼっていたファクシミリ受信用紙枚数が16年には約3800枚と半分以下に削減されている。同社は国際品質管理規格「ISO9001」を2000年に取得しているが、03年から同規格の維持に必要な膨大な文書もすべてサーバー内で管理するようにしたので、「非常に楽だ」(山口社長)という。決算書類など経営管理に必要な文書も、サーバー内の階層別ホルダーに収納。書棚に並べてある文書ホルダーよりもスピーディーに取り出せるし、閲覧できる人を限定するなどセキュリティーも確保できる。
山口製作所の頭文字をとって「YSSネットワーク」と呼ぶ社内ネットワークには、現在、各種工作機械、測定機をはじめ、タブレット、パソコン、プリンターなど100台以上のクライアントが一つのサーバーにつながっている。その数は同社の従業員数の3倍以上にのぼる。このネットワーク上で稼働しているシステムは日々、進歩しており、現在の生産管理システムは、最初に受注データを入力すると、材料の注文から生産計画の策定、在庫管理、納品処理までを一括管理できる。
同社の受注件数は月平均約750件。このうち取引先から紙の注文書がファクシミリで送られてくるケースが約60%、電子メールでデータを送ってくるケースが35%程度、残りはその他といったところだが、いずれもプリントアウトすることなくパソコン上で入力処理する。すると、受注した製品をつくるのに必要な材料や部品の在庫状況を確認し、足りないものを調達するための発注書が作成される。さらに、使用する機械の種類やリードタイム、作業ルール、生産数量などの生産計画を弾き出し、その後の在庫の状況や納品伝票作成までを自動的に行う仕組みだ。かつては、受注、生産、出荷、納品の各段階で手入力による作業が必要だったが、現在は受注段階でのみ手入力をすれば、自動的に生産計画が立ち上がる。
「プログラムを内製しているので、効率化を図れるところはどんどんプログラムを増やしていける」。こう語る山口社長が目標とするのは、「手による入力作業は極力やめよう」ということだ。
製造現場もコンピューター化推進
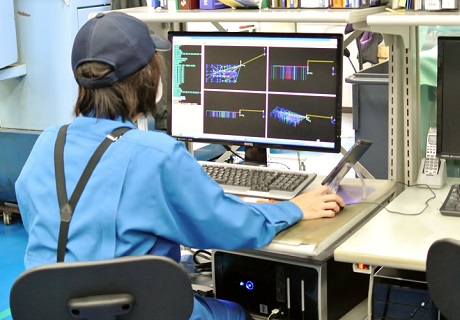
製造現場のIT化も徹底。いち早くCNC測定機を導入したのは、「若くして経営者になり、経験と実績がなかったので、測定機の絶対値にこだわるような品質管理をしたかった」(山口社長)からだという。ちなみに測定機は金型部品の精度を測定・評価するのに使われる。現在は3次元の形状を短時間で測定する最新型の自動測定機を稼働。最近は測定する金型部品のCAD情報をもとに、測定機が自動的に測定プログラムを生成する機種を導入し、一段と自動化を進めている。
また、同社ではマシニングセンター(MC)でちょっとした穴を1つ開けるのにも、MC本体のキーボードで操作するのではなく、必ずCAMからデータを送るようにしているという。これにより、専門教育を受けた人材でなくとも、ミスのない確実な操作が可能になるからだ。実際、同社に入社する前はスーパーでレジ打ちをしていた女性がMCのオペレーターとして活躍している。
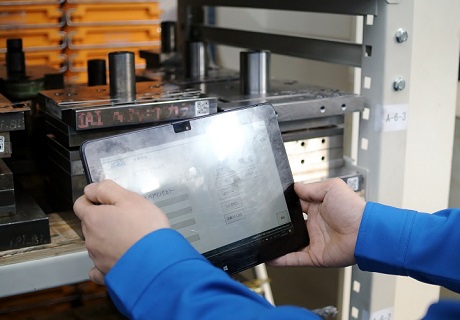
製造現場の作業員は、それぞれタブレットを保有。タブレットのQRリーダーで金型部品のQRコードを読み取り、その部品を使った作業内容を入力するなど、異常報告なども含めて何か作業をするたびに使用した機械など必要事項を入力していくことで、1日の作業日報が自動的に作成できる。それらを一覧できる画面の閲覧権限を持つ管理者は、誰がどんな仕事をしたのかがひと目でわかるし、社員の客観性のある業績評価が可能になる。
生産性が約3倍に向上
また、IoTを活用したプレス機の稼働状況に関するデータ取得システムを導入するに際しては、製造業向けIoT製品メーカーで技術コンサルタント会社の株式会社KMC(神奈川県川崎市)と連携、IoT対応ではない古いプレス機でも後から付けたセンサーのデータを読み取ることでIoT対応にするツール「Σ軍師」などを導入して、実現した。現在、8台のプレス機のショット数やプレス荷重変動、稼働率などのデータを収集、分析。不良品が発生する前に不具合を発見することで、不具合の対応費用やプレス機停止時間の削減に役立てるととともに、近年、顧客からの要望が強まっているトレーサビリティーを実現することで、顧客からの信頼性向上につなげている。
プレス機のIoT化にあたっては、KMCが経済産業省の平成27年度補正予算による「ものづくり・商業・サービス新展開支援補助金」を活用している。
山口製作所は、これら最新鋭の設備とテクノロジーにより、高精度・短納期を実現。とくに精密順送プレス金型については他社と比較して7~8割の短納期を誇る。IT化に取り組まなかった場合に比べ、生産性は約3倍に向上したとみている。同時に、コントロールエラー(CE=管理ミス)ゼロを目指す「CE ZERO(セゼロと発音)」を合言葉に品質管理も向上。山口社長は「品質データを手書きや手入力にしているとヒューマンミス(人為的ミス)が避けられないが、機械から直接データを入力できるようにすればかなりエラーを減らせる」と語り、これからも「受注1件のデータ処理は1回の手入力で済ませる」をコンセプトにIT化、IoT化に取り組んでいく方針だ。
企業データ
- 企業名
- 株式会社山口製作所
- Webサイト
- 法人番号
- 9110001025514
- 所在地
- 新潟県小千谷市片貝町10245-1
- 事業内容
- 金型製作、プレス加工