BreakThrough 企業インタビュー
中小企業を、IoTでスマートファクトリーに!昭和の工場も「製造ライン遠隔モニタリングシステム」で生産性アップ【i Smart Technologies 株式会社】
2018年 8月 30日
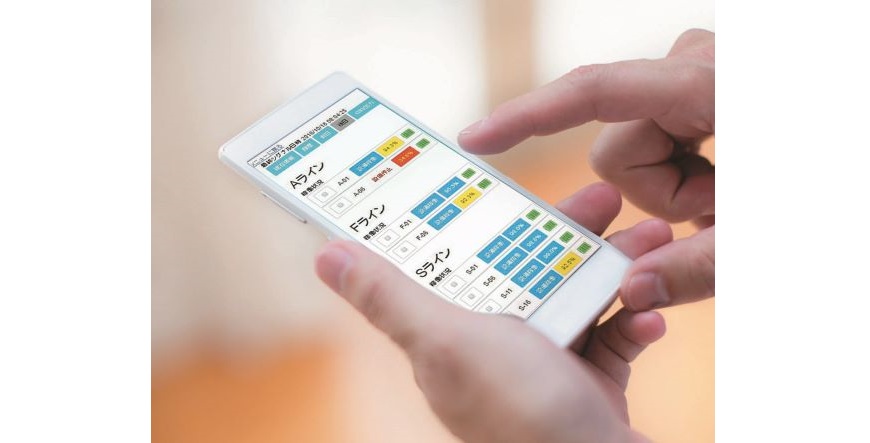
summary
正確な現状把握と改善の運用で、生産性を大幅アップ
改善活動の実績を元に、新会社を設立。他社へもサービスを展開
シンプルな構造のIoTを広めることで、中小企業のスマートファクトリー化をけん引
i Smart Technologies株式会社(以下、iSTC)は、中小企業のスマートファクトリー化をけん引するため、オリジナルのIoTシステムを広めようと設立された。
その基となったのは、自動車部品メーカーである旭鉄工株式会社での改善活動だ。旭鉄工では、より正確な現状把握のためにIoTを利用した自動モニタリングシステムを開発し、運用することで大きな成果が上がった。そこで、ほかの中小企業にもIoTの活用を広めたいと、iSTCを立ち上げたのだ。開発の経緯から振り返る。
データ収集は、IoTを活用した自動モニタリングシステムで
旭鉄工は、取引先から増産依頼を受けた際、設備の増設ではなく生産性の向上で対応できないかと考えた。そのためには、改善活動が欠かせない。だが一方で、改善の第一歩とされる現状把握を正確に行えないという問題も抱えていた。当時、1時間毎の生産個数やラインの停止時間などのデータ記録は、製造ラインの担当者が様々な業務と兼任しながら実施しており、正確なデータの収集は難しかった。そこで、IoTを活用した自動モニタリングシステムの導入を目指すことにしたのだ。
当初は、既存の製品を探した。しかし、システムが大掛かりで高コストな上、最新設備とは言いがたい“昭和の工場”に使えるものが見つからなかった。ならば「自分たちで作ろう」と開発に踏み出した。
旭鉄工が開発した自動モニタリングシステムはシンプルな構成だ。例えば、製品が1つできるたびに、シグナルタワーが点灯する機械なら光センサーを、安全扉の開閉など動きのある機械には磁気センサーを取り付け、パルス信号を発生させる。パルスの数が「生産個数」を、パルスの間隔が「サイクルタイム」を表す。また、パルスの間隔が一定以上長くなると、ラインが停止したと考えられる。こうした情報がクラウドを経由して担当者のスマホや社内のモニターに届くのだ。
なお、これらのセンサーは、秋葉原で購入した1つ50円の光センサーや、250円の磁気センサーというから、実に低コストである。
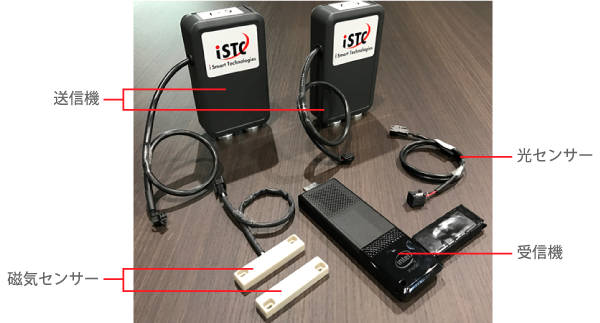
見える化だけでは解決しない
旭鉄工では、IoTは、IT(Information Technology)とOT(Operation Technology)の両輪で成り立つと考えている。ITで正確な現状把握ができたとしても、重要なのはその先だ。データから問題点を洗い出し、どう改善し、運用(Operation)に結び付けるか。「それが付加価値の高い、人にしかできない仕事だ」と旭鉄工の代表取締役社長であり、i Smart Technologies 株式会社の代表取締役社長CEOを兼任する木村哲也氏は言う。
とはいえ改善は、一朝一夕には進まない。旭鉄工では毎日、部長などの責任者と担当者らが現場に集まり、ラインの停止理由やその対策を話し合った。当初は、毎日のミーティングが数時間に及び、社長も参加してアイデアを出した。小さな工夫の積み重ねが大切だが、ときに先入観のない突飛とも思える意見が問題解決の突破口になることもある。
その結果、旭鉄工の出来高は、2014年に「製造ライン遠隔モニタリングシステム」を導入して以降、80ラインで平均34%、最大128%アップした。約4億円の設備投資と、年1億円以上の労務費の削減にも成功し、平日の残業ゼロも達成した。
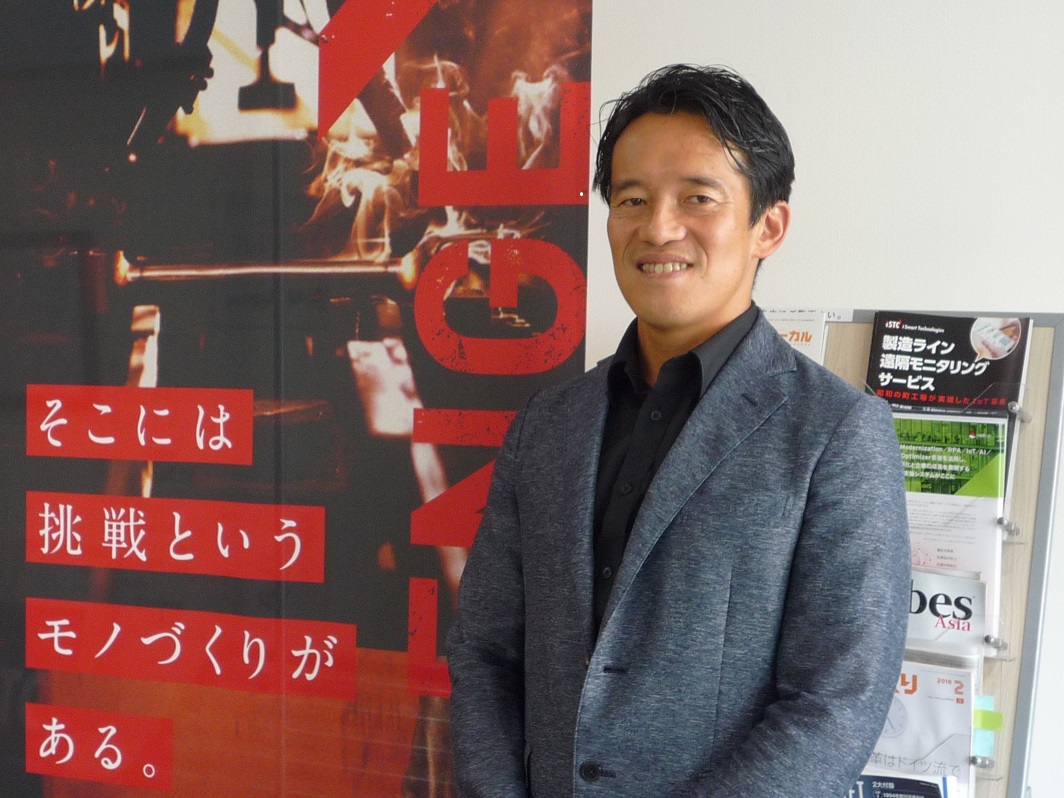
IoTは、中小企業にこそ必要
旭鉄工での成果を踏まえ、木村社長は「このシステムなら、他社にも運用できる」と考え、2016年9月にiSTCを立ち上げた。
iSTCは、製造ライン遠隔モニタリングシステムを、初期投資が約10万円、月間利用料は5ラインで39,800円と、中小企業にも負担の少ない料金設定で提供する。設置から長期間経た機械への導入も問題なく、「中小企業の生産性向上」をサポートする。
しかし、システムを導入しデータが揃っても、改善方法の見当がつかない企業も多い。そこで、iSTCは「データ解析サービス」を開始。導入企業の5日分のデータを元に、問題点を見つけ、改善策やその考え方をレクチャーする。それらが活用できれば、独自解析による改善策を講じて、時間当たりの出来高が3カ月で59%アップした例もあるという。
「中小企業は生産性向上の余地が大きいし、小回りが利く。中小企業こそIoTを使った変革が成功しやすい。挑戦するべき」と木村社長は言う。
チャレンジ精神でイノベーションを起こす
iSTCのシステムは、サービス開始から約1年で、導入企業は100社にのぼる。業種は、金型加工や塗装業、菓子製造、製薬工場など多種多様だが、約80%が中小企業だ。
今後は、2020年までに累計2000社の導入を目指している。木村社長は「厳しい目標だが、中小企業のIoT化を推進するために必要な目標値だ」という。
また、新たにアマゾンウェブサービスのスマートスピーカーなどの活用したソリューション開発を進め、旭鉄工で試験導入を始めた。材料の補充などで製造ラインを停止するとき、これまでは作業者が手袋を脱ぎ、タブレット端末に停止状況を入力していた。しかし、スマートスピーカーがあれば、「アレクサ、設備切り替えをして」などと話しかけるだけで入力が完了する。作業を中断することもなく、停止時間の短縮に効果が大きい。勤怠管理への活用も含め、サービス展開を検討中だ。
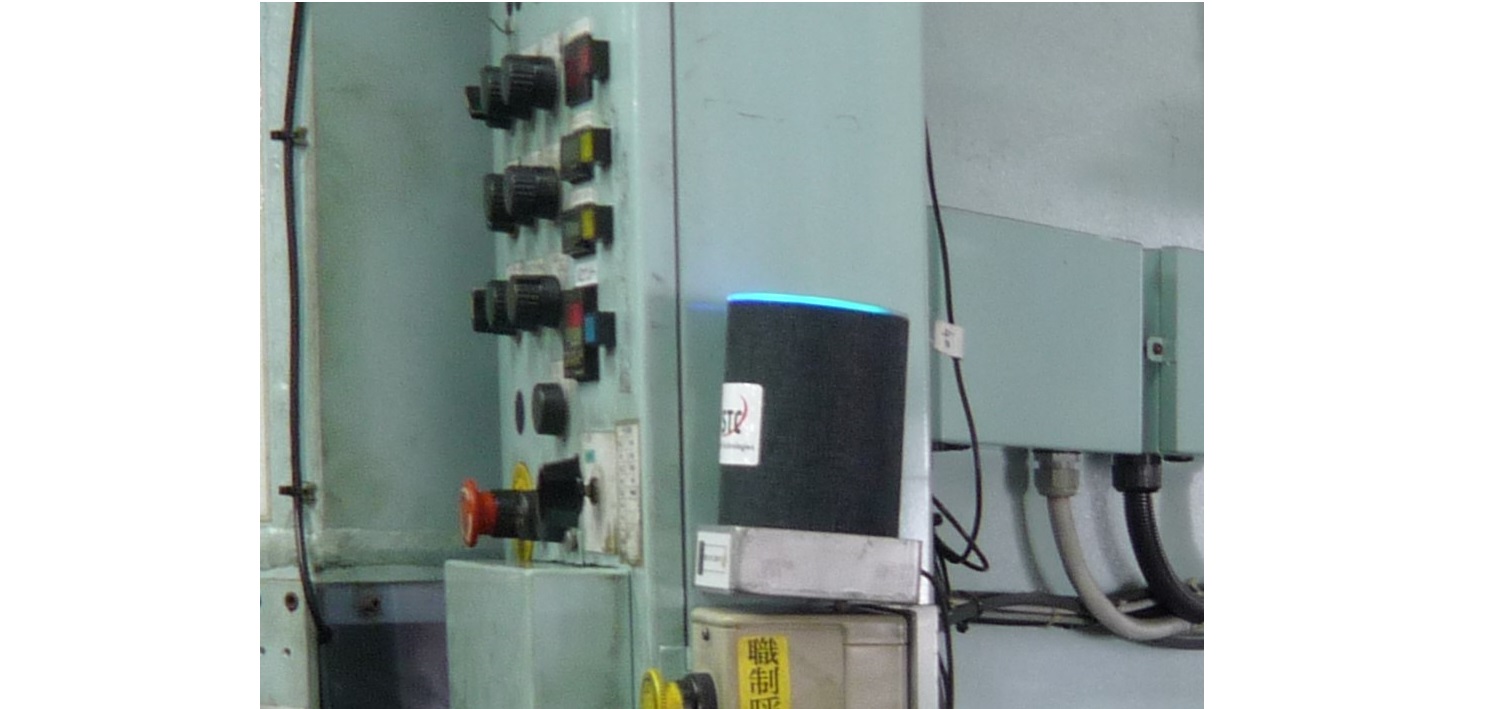
こうした最新機能の開発は、社員の「おもしろそう」というひらめきからスタートすることが多いという。興味のあること、新しいことにチャレンジする社内風土が、更なるイノベーションを起こしていくのだろう。
iSTCはタイ政府とも相互協力をし、2017年からタイ国内8社で実証実験を始めている。日本国内にとどまらず、世界の工場の「industry4.0」をけん引する今後の活躍に注目したい。
企業データ
- 企業名
- i Smart Technologies 株式会社
「中小企業の生産性向上」をミッションとして、中小企業でも導入しやすいIoT「製造ライン遠隔モニタリングシステム」を提供しています。また、稼働状況のデータ分析やコンサルティングのほか、講演会やワークショップなどを通じて、改善力の養成や人材育成も支援しています。2018年1月には第7回「ものづくり日本大賞特別賞」、5月には「SMART FACTORY AWARD 2018」などを受賞しました。
取材日:2018年7月31日